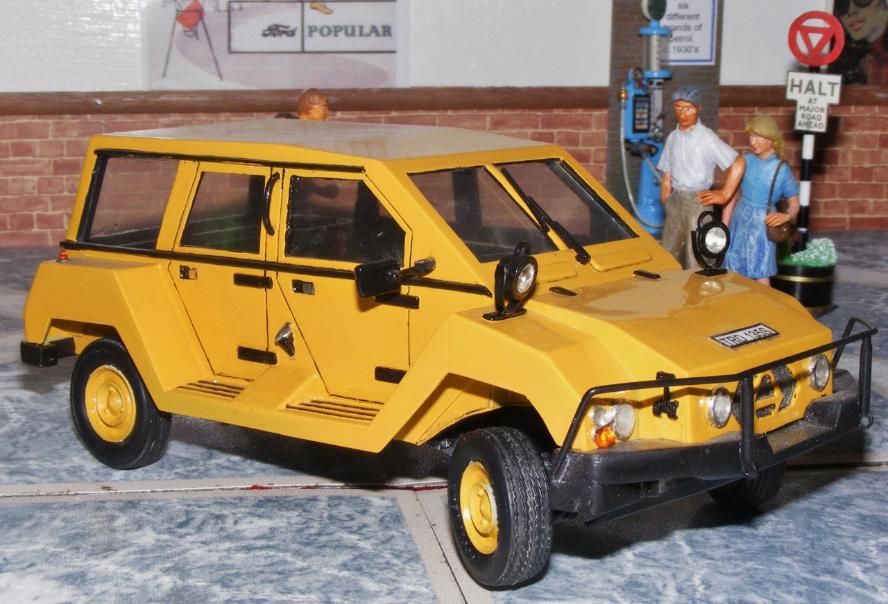
1984 Africar Mk.3 wagon.
The Africar was an attempt by English journalist and photographer Tony Howarth to create car, suitable for the African continent, with all its attendant problems, that could be cheaply produced in Africa, by Africans, and be sold across Africa and anywhere else that “roads” don’t exist.
However, the Africar was much more than the paternal white view of African needs and abilities. It’s wooden construction, and development of a combination of efficient Diesel engine and electric motor with 16% solar panels adding energy to on-board batteries, made it ecologically friendly decades before the hybrid idea became fashionable. When you look at the Africar, it’s design ideology, off road abilities with a very smooth on road ride, the Africar could be considered the original “crossover” car, even it’s generally large appearance fits the bill.
Tony Howarth travelled extensively in his work as a journalist, photographer and film maker. His credentials in this area are pretty good; Hollywood Film Society’s Award of Excellence, Blue and red ribbons at the American Film Festival and Golden Globe and Oscar nominations. While travelling on a terrible northern Zambian road in 1964 Howarth had the thought that there must be a better vehicle to tackle these awful roads. The idea grew through his visits to 112 countries on 6 continents and his response to automobile companies from around the world selling unsuitable cars to countries without metalled roads, leading to the vehicles being destroyed before the purchaser had finished paying for them, was not good. After years of gathering more and more ideas for a suitable type of vehicle design the real research was carried out through 1979 and 1980. This was followed up with a specially study into the relevance of the motor car across the whole world, not just the industrialised countries with developed road networks.
What Howarth found was that the needs of the undeveloped parts of the world were very different from those of the western world, and although he misunderstood some of these differences his 1983 design, conceived over 4 months in Coalville, Leicestershire, was functional, strong and ground breaking.
Like other off-road attempts, the Baby-Brousse and Mehari, the Africar utilised many aspects of the legendary Citroën 2CV. It was conceived as cheap to make and easy to repair and maintain with the minimum of knowledge and tools. Unlike the metal bodied Brousse or the ABS plastic body of the Méhari the Africar has an epoxyresin saturated plywood body, something aircraft and boat-building industries had been using for decades. With no curves in the design the wood sections were thought to be easy to repair individually and as Howarth intended that these vehicles be made in small local factories, easy to produce with a low skilled work force. This was one of his misunderstandings that led to the failure of the product. The Africans feeling patronised and undervalued, decided they didn’t need his Africar design anyway. Had Howarth approached the prospect from a different angle he might have had more success but the fact is, the vehicle was a sound design and proved it too.
The historic and revolutionary Africar was a totally new design. Although often reported as based on the Citroën 2CV that isn’t an accurate statement. Howarth did use the lightweight Citroen GS 1300cc 4-cylinder air-cooled boxer engines,Citroën GS van low ratio 5-speed gearboxes and Citroën drivetrains, as the basis of the early Africars these were modified. For instance, although the wheels came from Citroën they were widened to allow for the suspension geometry Howarth required to create zero scrub steering. Even the exhaust pipes were altered, not just to improve performance but by using Stainless steel protection against corrosion was maximised in this vulnerable area.
Ground clearance required the front hubs to have drop ratio gearboxes in order to keep the drive shafts horizontal and centred to the wheels. This require the front brakes to be mounted in-board, which keeps un-sprung weight down and centralise weight to aid handling.
Other elements came from different companies like British Leyland's Hydrolastic suspension system but all these mechanical parts were seen by Howarth as stopgaps while Africar developed their own components.
The obvious visual aspect is the body shape but the entire chassis is made in the same way; by saturating plywood with epoxyresin. This system has been used in the aircraft and boat-building industries for many years, most notably by "West" who used in the construction of yachts. West, worked with Howarth in the design and specifications of the Africar to construct a relatively lightweight (1000kg), but very sturdy, vehicle. Most importantly it was cheap and could be repaired with minimal tools and locally available wood.
The chassis and body were designed with all the problems of off road driving. The Africar has more ground clearance than a Hummer and more space in the wheel wells than most, if not all, modern SUV. The wide track and flat bottom eased passage over rough and muddy roads while the rising rate suspension and 350mm of vertical wheel movement not only helped the Africar cope with ruts and potholes but gave unparalleled ride comfort on paved roads. Add to this the great load carrying capacity and you have a truly great vehicle for pioneering drivers.
As the designs developed and the other models were added to the line-up other ideas were incorporated. The all-wheel drive Wagon version had a composite Solar Electric Diesel drive system, what we today call hybrid drive, which was pioneering in the early 1980s.
The final step in protection of the vehicle was the use of Glasurit’s top level paint systems to give the final seal and weatherproofing.
Sadly, very few drawings or plans for these innovative designs are available. This is partly down to Howarth himself subduing the availability of plans to protect his rights during patent applications and partly down to the disastrous collapse of Africar International Ltd. and the usual disorganised sales of any assets to pay off some debts.
After all the information gathering the ideas started to become a reality when the first prototype, nicknamed “Bessy”, was built in 1982. A second vehicle followed and in 1983 four 3rd generation prototypes were built so there was a pickup, a station wagon and six wheeled version. Of course the established motor manufacturers, those that bothered to even acknowledge the Africar, scoffed and critics were many but Howarth and his supporters pushed ahead anyway. The Africars would need to prove ability and ensure the world would see it.
At the end of 1983 an Africar pick-up took part in the thousand-mile Himalayan rally. Unfortunately, the vehicle failed to finish due to an overheating fuel pump starving the engine of fuel. However, the Africar was in 7th place at the time ahead of a turbo Range Rover, 3L Volvo, Subarus, and several Escorts. The 65hp vehicle was also good enough to record 5th fastest time on some competitive sections too.
A much more well-known event was a testing and promotional endurance drive from Arctic Circle area of Norway to the African Equator, considering there was to be no back up to the team this was a risky adventure. A standard Africar, the pick-up version and the 6-wheeler took 4 months to complete the journey and all three vehicles were in good condition at the end. After the run the three cars were examined by representatives of nine countries in Nairobi. This journey was filmed by Howarth as a documentary for promotional purposes and was also a large section of the “Africar” book. In May 1987 Channel 4 broadcast “A car for Africa”, a 5-part series of 60 min’ episodes, on British television. Showing how the Africars made the journey and stood up to the challenge, these programmes also raise a lot of interest and awareness amongst potential backers.
With the concept proved and backers starting to come forward Tony Howarth founded "Africar International Ltd" in September 1986. Based in Lancaster from 1986 to 1988 AIL was to build a range of different vehicles, including the all-wheel drive car and an eight-wheeled drive panel van. The aim was to get production up and running then set up small factories around the world where local people could build the vehicles and respond to local needs better, and more quickly, than the world’s large vehicle producers. Retooling traditional car manufacturing plants would be too much to be cost effective. However, the locally produced vehicles would be more affordable and better suited to the environment they were to be used in, than vehicles originally designed for tarmac roads. It would also be a move away from steel, plastics and fibreglass (both of which are equally inappropriate in rugged, hot environments) to a renewable and easily workable material.
At the time there were a lot of companies interested the idea, whether it was for financial benefits or because they saw the ecological and sociological benefits. Whatever the reason for the backer’s and customer’s interest everyone was impressed with the vehicles capabilities.
Having seen the Channel 4 programmes customers put down deposits, but Tony Howarth’s ambitions outstripped his resources and business abilities. Delivery dates kept being delayed as AIL struggled to develop their own power, transmission and suspension systems. Things got so bad that by December 1987 AIL was reduced to the ruse of roping off a dummy vehicle at a Christmas party thrown at the Lancaster works. It had been intended to impress people and garner more deposits to tide the company over, later others were to see it as misrepresentation and even outright fraud.
Howarth attempted to float AIL as a public company selling shares, the desired £5 million didn’t materialise and the February ’88 flop effectively killed the company. With no completed cars, and unable to pay its creditors, investors or staff, AIL was raided by Lancashire Constabulary’s Commerce Branch who seized the company's documents and allowed the landlord recover possession of the factory building on the 18th of July 1988.
Only 6 Africars were built and the only customer who took possession of one did so by driving it away without permission!
At the time Tony Howarth was in the USA seeking out more investors to try and keep his dream alive. He didn’t return to the UK until October 1994 and was then arrested and charged with numerous offences. The bankruptcy court had sold off all AIL assets and Howarth was now imprisoned for 15 months having pleaded guilty fraudulent trading and obtaining property by deception.
Legacy
If the end of AIL was tragic and Howarth’s imprisonment and ruined reputation rather sordid the Africar itself was a real piece of progressive automobile technology. The failure of AIL can be put down to a number of things mostly around Tony Howarth’s deficits as a businessman. The idea was put to many financial backers but the people and organisations concerned with helping Africa were hardly aware of the project, a lot of possible support and credence was lost but not using this resource both financially speaking and in helping shape the idea to include the views of the African people themselves. By not testing the market forces properly a lot of prospective local buyers saw the Africar as hangover of the colonial attitudes, a white man’s paternalistic view of we know best what Africa needs.
However, the design ideas created an exceptional vehicle for use both off, and on, the road. It pioneered an ecological ethos in the use of wood and combinations of efficient engines and solar electric drive was way ahead of its time. Perhaps if Howarth had stayed within his resources instead of chasing the sun the Africar might have had more of a chance.
Although the Africar project was un-successful the design influenced other car designers and companies and is still studied today during the search for efficient ecologically friendly motor vehicles.
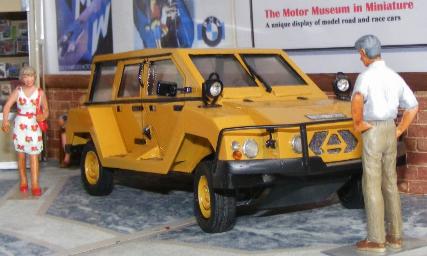
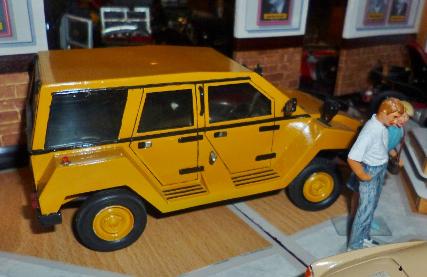
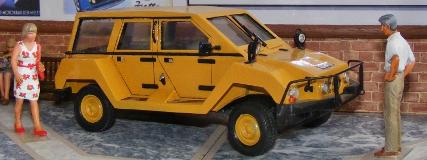
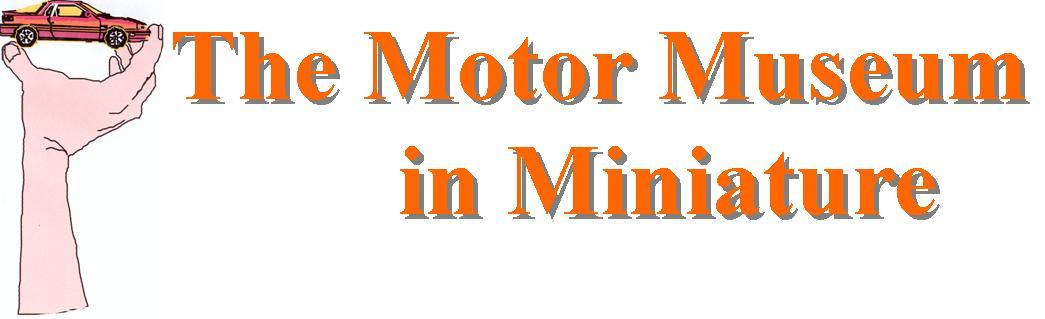
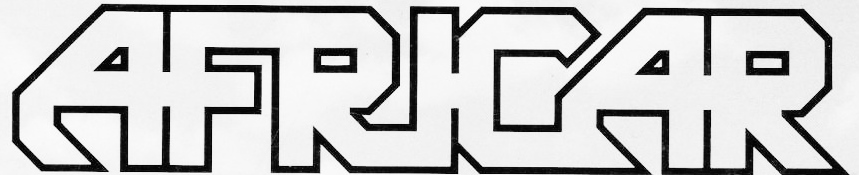
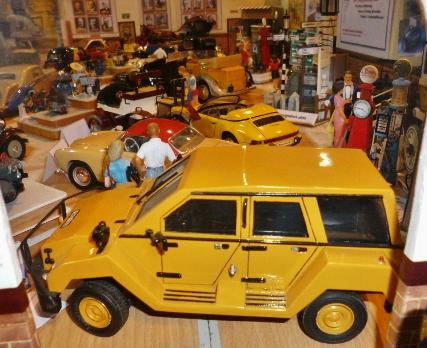

Scratch built over the winter of 2008/09 the body is entirely made from plasticard. Almost everything had to be made in this way due to the unique design of the vehicle. The few production kit parts used, most of them modified in one way or another, came from the Imai 2cv kit, Imai kit # B-867-700 (sometimes listed as B-867, B-2508/9 or FA-130) although some bits were scavenged from the bits box
The body and most parts are painted with Halfords acrylic car spray paints. Other paints used were Citadel acrylic paints and washes from the Games Workshop and Humbrol enamels.
RETURN TO :-